The ideal choice for pressurised piping systems
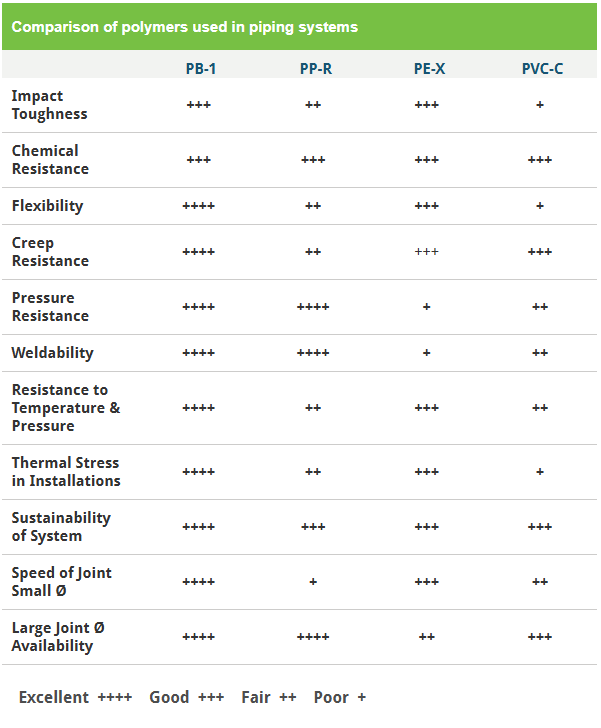
The property combination setting PB-1 apart from competitive materials is its high flexibility combined with outstanding resistance to internal pressure creep resistance over a wide range of temperatures.
The unique morphology and crystallisation behaviour of PB-1 gives it unrivalled properties for pressurised piping systems.
All polyolefinic materials tend to creep when exposed to continuous stress over a long periods of time.
This cold flow behaviour can be suppressed by creating a 3-D network in the polymer structure such as the physical and chemical linking utilised in the manufacture of Polyethylene (PE-X). Polybutene-1 however, displays superior inherent creep resistance (see table below) without the need to apply any additional cross linking, copolymerisation or compounding modification.
In its simplest homopolymer form, the property profile of Polybutene-1 makes it the ideal choice for satisfying the demands of hot and cold pressure piping systems applications.
The performance comparison of PB-1 and alternative plastics materials
Parallel standards to ISO 12230 exist which present the effect of time and temperature on the expected strength of the materials listed below. The data presented in these standards provides a useful means of comparison of the performance of these alternative plastic materials used for piping systems.
The following figure shows the performance reference lines (pressure resistance properties) for the following materials at 70°C on an equivalent scale:
Best performing materials
- PB-H | ISO 12230 (2012)
- PB-R | ISO 12230 (2012)
Medium performing materials without knee point
- PE-X - ISO 15875 (2003)
- PP-RCT - ISO 15874 (2013)
- PE-RT type II - ISO 12230 (2012)
Low performing materials with knee point
- PE-RT type I - ISO 22391 (2009)
- PP-R - ISO 15874 (2013)
After 10 years of exposure to continuously applied stress, the best performing Polybutene-1 (PB-H & PB-R) retains over 50% more strength than the medium performing materials (PE-X, PP-RCT & PE-RT type II) and 70% - 90% more strength than the lower performing materials PE-RT type I and PP-R.
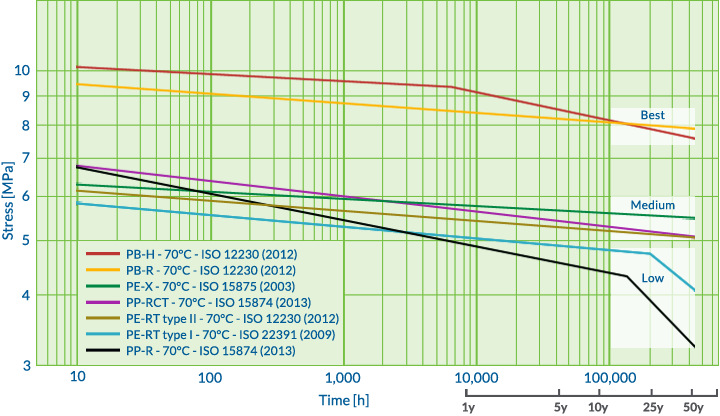
Design stress
After 10 years of continuously applied stress, PB-1 retains over 50% more strength than PE-X, PP-RCT and PE-RT type II, and 70-90% more strength than PE-RT type I and PP-R.
By employing standardised dimensional criteria presented in ISO 10508 it is possible to calculate the maximum allowable hoop stress of these alternative polyolefin pipes for the various standardised applicational temperature classes. This calculation of design stress results in the comparison presented in the table below which shows that PB-1 polymers achieve the highest hoop stress values across all standardised application classes. The intrinsic stress bearing advantage of PB-1 is between 35% and 90% higher, depending on application class and material. This effectively means that at equivalent thickness, PB-1 pipes offer a significant safety factor over these alternative plastic materials for installed systems.
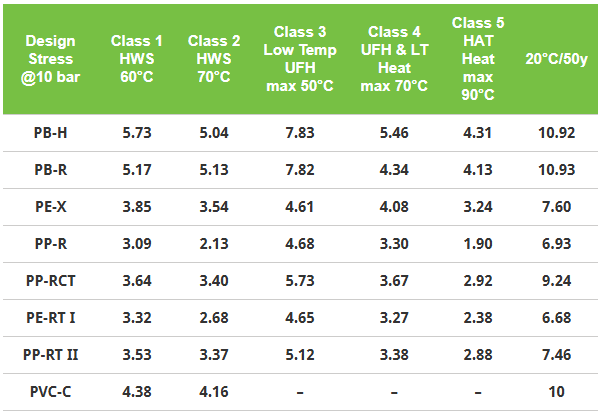
From the maximum allowable hoop stress, we can calculate a minimum allowable wall thickness. It is clear from the calculation that Polybutene-1 pipes can be produced with a significantly reduced wall thickness when compared to other materials dependent on applicational standards limitations. Lower wall thickness also means a larger internal bore for a given external pipe diameter resulting in reduced head pressure loss and lower flow speeds to deliver a fixed volume of water.
*PE-RT denotes Raised Temperature Resistance polyethylene
Superior long term creep resistance
In contrast to other thermoplastics used in piping applications, performance modification via compounding, cross-linking or copolymerisation is not necessary for PB-1 piping systems to fulfil the stringent performance standards applied to their use.
In comparison with other polyolefin materials, Polybutene-1 has a higher level of resistance to strain under continually applied stress over long periods of time. This is known as creep behaviour and the graph illustrates the superior performance of PB-1 at times in excess of 100 hours.
In addition to its excellent mechanical and thermal properties, PB-1 provides a high level of resistance to chemical attack and also offers a level of flammability resistance meeting the demands of most applications.
PB-1 can be processed via standard injection moulding or extrusion processes into a broad range of products. In its most simple homopolymer form, the balance of properties of PB-1 make it the technically preferred material for the production of pressurised hot and cold water piping systems.
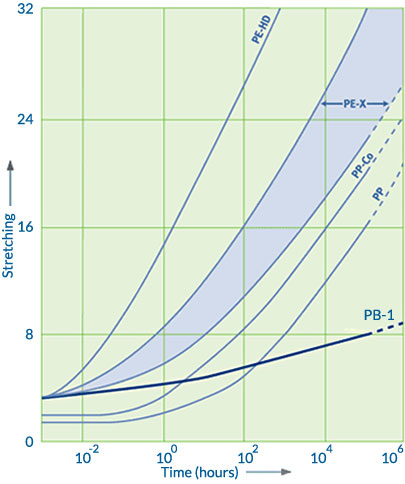
Pipe weight and hydrostatic efficiency
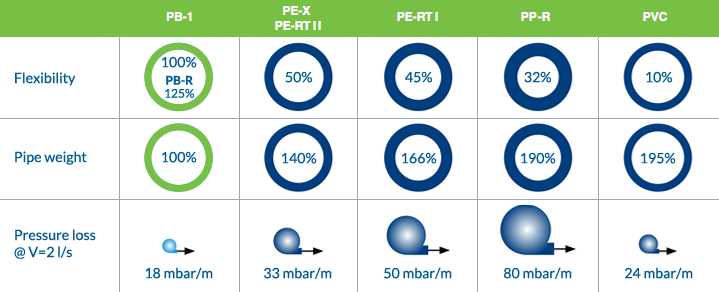
Calculated for application class 2, 10 bar design pressure, based on published data.
Sound dampening
The thinner pipe walls, high elasticity and low specific density in PB-1 pipes leads to high absorption of operating noises.
Among the superior properties of Polybutene-1 in comparison with other materials its excellent sound dampening. The combination of thinner pipe wall construction, low elastic modulus and low specific density in Polybutene-1 pipes (ρ = 0.9 g/cm3) leads to high absorption of “water hammer” and other noises associated with heating and cooling in pipe systems. Tests showed a 90% reduction of pipe-borne noise in the Royal Albert Hall in London after the installation of PB-1 pipes.
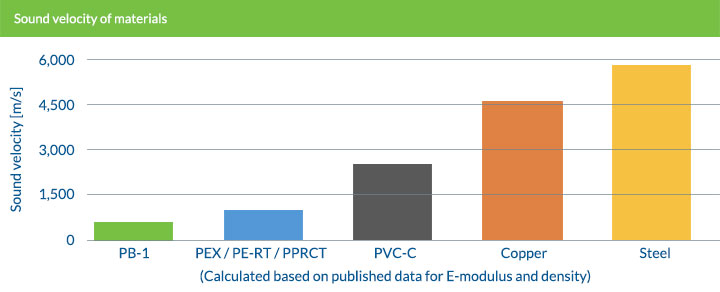
Water Hammer
The higher the SDR Class the lower the water hammer at a given flow rate. PB-1 has the highest SDR Class compared to PP-H, PP-R PE-RT and PEX
A column of moving water within a pipeline contains stored kinetic energy arising from its mass and velocity. Since water is essentially incompressible, this energy cannot be absorbed when a valve is suddenly closed.
The result is a high instantaneous pressure surge normally referred to as 'Water Hammer'.
With people living together in greater density the noise levels and acoustic properties of piping systems are a significant issue. Piping systems that minimise fluid noise and water hammer where pipework passes through ceilings and walls are a key element in addressing residents’ noise concerns.
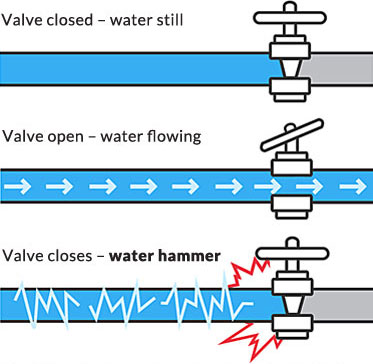
Five factors determine the severity of water hammer:
- Velocity
- Modulus of elasticity of the pipe material
- Inside diameter of the pipe
- Wall thickness of the pipe
- Valve closing time
Repetitive water hammer can be destructive to pipe systems. Beside the noise, water hammer can cause pipelines to break if the pressure is high enough.
The maximum theoretical value of pressure surge Ps is:
v0 · a · ρ = ps
v0 = velocity of the medium [m/s]
a = propagation rate of the pressure wave [m/s]
ρ = density of the medium [kg/m³]
ps = pressure surge – water hammer [N/m²]
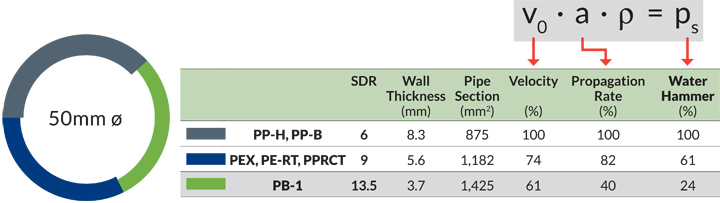
The maximum surge pressures caused by water hammer can be calculated using the following equation taken from the 'Handbook of Thermoplastic Piping System Design', Thomas Sixsmith and Reinhard Hanselka, Marcel Dekker Inc., pp 65-69
Ps = V((3960 E t)/(E t + 3 x 105 DI))½
where:
Ps = surge pressure (psi)
V = water velocity (ft/sec)
DI = inside diameter of the pipe (in)
E = modulus of elasticity of the pipe material (psi)
t = pipe wall thickness (in)
The low elastic modulus of Polybutene-1, combined with reduced wall thickness gives rise to a low surge pressure for a given pipe OD and pressure rating. The table below compares maximum surge pressure for 38.1 mm (1-1/2") OD pipes of different plastic materials, designed for the same pressure service.
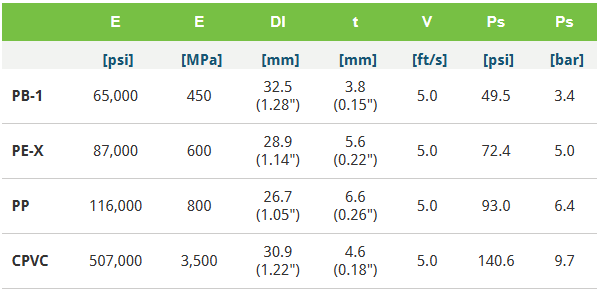
When compared to PP-H, PP-B, PE-RT and PEX, PB-1 has the highest SDR Class and delivers the best acoustic capabilities including the lowest level of water hammer.
Polybutene-1 offers tangible benefits for piping systems compared to PE-RT and PEX
For building projects, the true cost variation of piping systems across competing materials is more than a per length cost comparison for the same outside pipe diameter.
Specifiers look at: ease of installation impacting onsite costs; jointing options, long-term system performance and projected life span; and Standard Dimension Ratio (SDR) comparing pipe materials for durability against pressure.
When compared to PE-RT and PEX systems, PB-1 offers significant benefits across a broad range of performance categories all contributing to make PB-1 piping systems the optimum choice for high performance piping installations.
Standard Dimension Ratio (SDR)
What is SDR?
SDR rates pipe durability against pressure and correlates a pipe's outside diameter and wall thickness.
The SDR or the Standard Dimension Ratio refers to the geometry of a pipe. SDR is a method of rating a pipe's durability against pressure and it describes the correlation between the pipe dimension and the thickness of the pipe wall. SDR 11, for example means that the outside diameter of the pipe is eleven times the thickness of the wall.
- High SDR ratio
The pipe wall is thin compared to the pipe diameter - Low SDR ratio
The pipe wall is thick compared to the pipe diameter
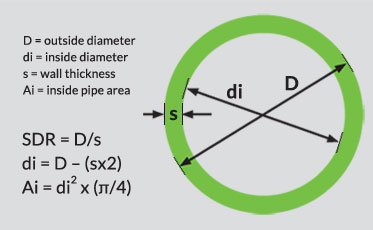
Example calculation:
SDR for a pipe with an outside diameter of 100mm and wall thickness of 5mm can be calculated as:
100mm / 5mm = SDR 20
Why does SDR matter for piping systems?
Due to the higher SDR ratio of PB-1 compared to either PE-RT and PEX, PB-1 piping systems deliver the following benefits because of its lower wall section requirements for the same pressure rating and outside pipe diameter:
- Less material for the same pressure capability
- Less weight per meter of pipe
- Lower outside pipe diameter for the same performance
- Larger inside area for the same outside diameter providing:
- Higher flow rate at the same pressure
- Lower pressure loss, requiring less energy to run a system or pumps with lower capacity
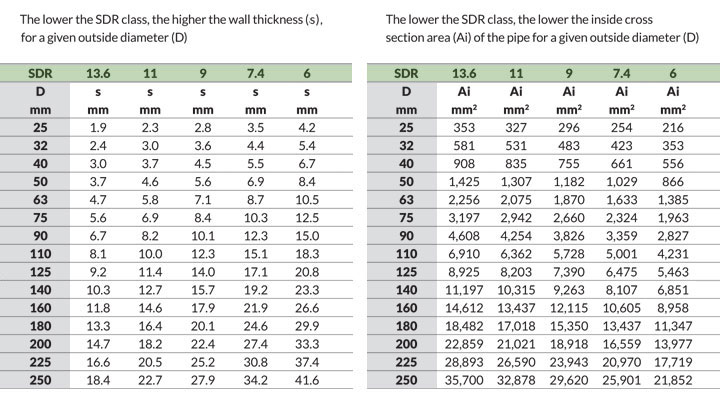
SDR Classes and Pipe Dimensions
SDR classes quoted in National Standards for District Energy piping systems
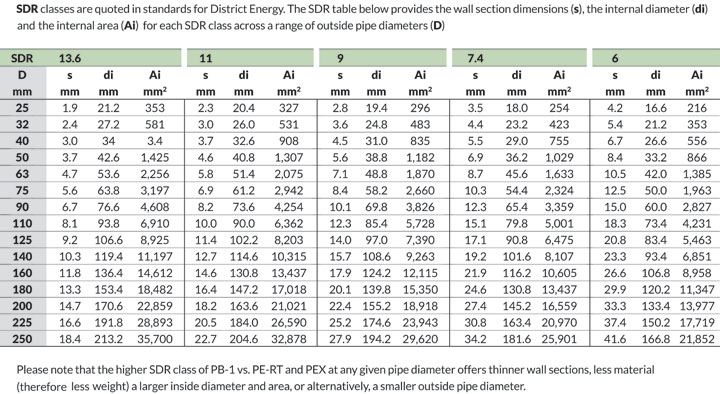
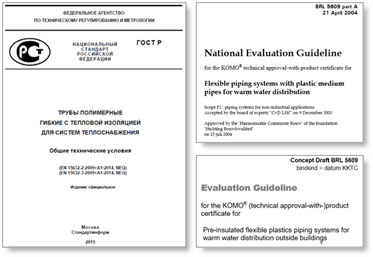
National Standards (RU & NL)
The source for piping dimensions comparing materials PB-1,
PE-RT and PEX
The current Russian standard for District Heating (GOST 56730 – 2015) and the Dutch guideline (BRL 5609 - and the draft of renewed BRL 5609) both include a comparison of 3 materials for District Heating piping systems: PB-1, PE-RT and PEX.
Both the Russian standard and the Dutch guideline have the same requirements in relation to the pipe dimensions and SDR classes of the 3 service pipe materials operating at pressures of 6 bar, 8 bar and 10 bar.
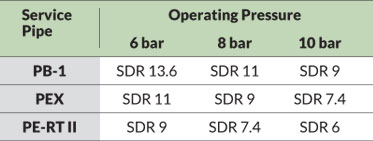
Per the Russian standard and the Dutch guideline the table (at right) is an excerpt of the relevant table showing the SDR classes for the listed materials at different pressure ratings. As indicated, for each operating pressure PB-1 is listed in the highest SDR class when compared to either PE-RT and PEX. The section below explains what this means, why standards refer to pipe dimensions and SDR classes and what are the benefits for pipe system specifiers.
Pipe Dimensions and SDR Classes
PB-1 pressure capability delivers benefits versus PE-RT and PEX
The higher SDR class of PB-1 delivers the following benefits:
• Thinner wall section
• Less material (less weight)
• Larger inside diameter and area
To illustrate the performance of PB-1, PE-RT and PEX in relation to the given operating pressure of 8 bar at the small pipe diameter of 50mm ø, the table and diagram below provide a comparison of the internal pipe dimensions required.
Example 1: Small pipe – 50mm diameter @ 8 bar
PB-1 is stronger than both PE-RT and PEX, and with an operating pressure of 8 bar and an outside pipe diameter of 50mm ø the required wall thicknesses are:
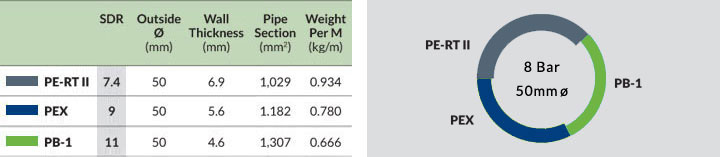
Per above, at the same water pressure, the larger inside diameter of PB-1 50mm outside ø pipe delivers a substantially higher flow rate than the other two materials. Taken the other way, at a given flow rate PB-1 pipes yield a lower pressure loss requiring less energy to run systems and/or pumps with a lower capacity.
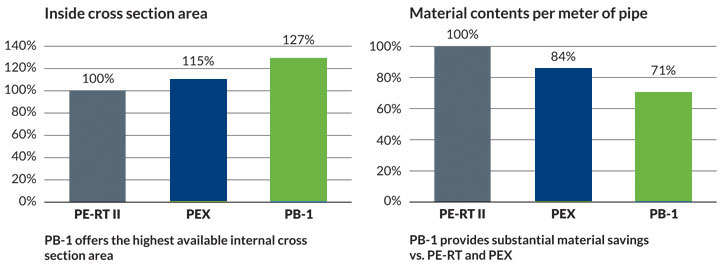
As shown in the graphs above and for the purposes of comparison, PE-RT may be considered the benchmark at 100%. When comparing the inside cross-section area of a 50mm ø pipe (left graph) PB-1 clearly outperforms PE-RT with an additional 27% of volume. Also, in comparing the amount of material per meter for a 50mm ø pipe rated for 8 bar (right graph), PB-1 pipe uses 29% less material than PE-RT.
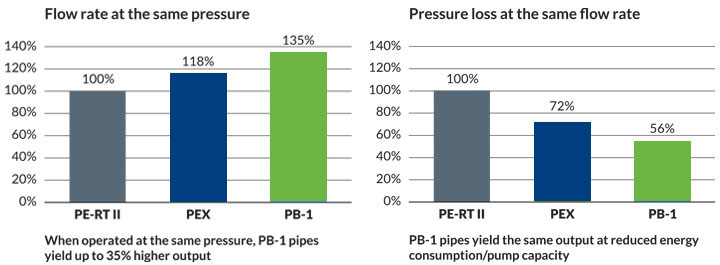
Once again for the purposes of comparison, PE-RT may be considered the benchmark at 100%. Per the above graph (left), using the same operating water pressure, a 50mm outside diameter pipe (8 bar) made from PB-1 delivers a substantially higher flow rate of +35% when compared to the identically rated PE-RT pipe of the same outside diameter.
Measured using the other comparison point (right): at a given flow rate (output) PB-1 pipes yield a 44% lower pressure loss versus PE-RT pipes. This means that PB-1 pipes require less energy to run a system - or - can accommodate pumps with a lower capacity for the same output.
Example 2: Large pipe – 160mm diameter @ 10 bar
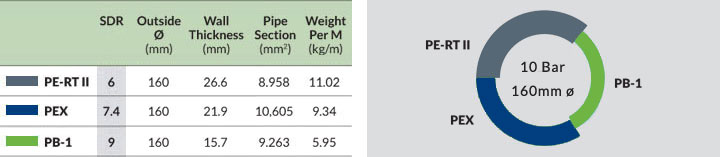
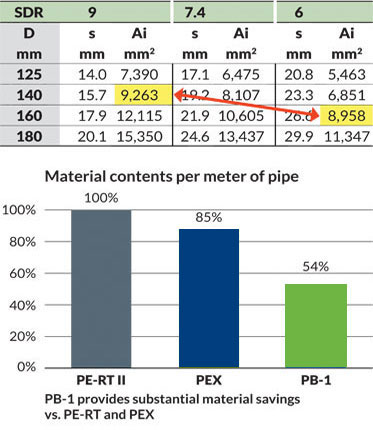
Due to a higher SDR rating (and therefore a thinner wall section) a PB-1 pipe of 140mm ø delivers the same performance as a PE-RT pipe of 160mm ø, but with a smaller outside diameter and larger inside pipe cross-section area.
At a 10 Bar operating pressure pipe of 160mm outside diameter:
- PE-RT @ SDR 6
160mm ø pipe has an internal cross section area of 8,958mm2 - PEX @ SDR 7.4
160mm ø pipe has an internal cross section area of 10,605mm2 - PB-1 @ SDR 9
With a smaller outside diameter of 140mm ø PB-1 has an internal cross section area of 9,263mm2
In addition, as shown in the graph (right), the weight of 160mm outside diameter PB-1 pipe rated for 10 bar is almost half of the weight for the same outside diameter and rating pipe made from PE-RT.
Jointing Techniques for Plastic Piping Systems
PB-1 is a versatile material for all available jointing techniques
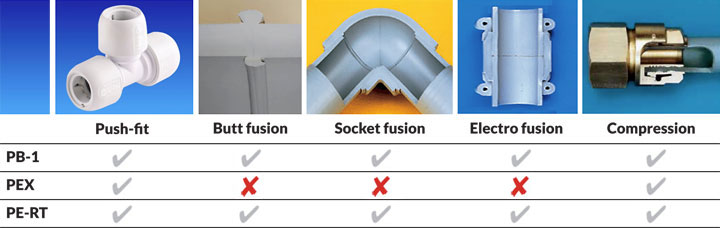
The Bottom Line
Specifying PB-1 piping systems offers:
- Substantial material saving opportunities, while at the same time increasing the capacity of the system
– thinner walls
– increase of the available inside cross section area - A higher degree of design freedom for projects including District Energy grids
– opportunity for using smaller outside pipe and fitting diameters - A clear opportunity for reduced integral installation cost and operating cost
– smaller pipe support frames
– use of less insulation material
– smaller pumps running at reduced energy consumption
– lighter overall weight for easier handling and lower shipping costs - The capability to utilize all available jointing techniques
- Best in class acoustics including the lowest level of water hammer
- The ability to be fully recycled
PB-1 vs. PE-RT & PEX
Webinar: Benefits of PB-1 for pressure piping systems
Business Review Webinars
- Sponsored by: LyondellBasell
- Presentation date: 7 March, 2019
- Presented by:
– Patrick van Beek, Marketing Manager PB-1
– Werner Rothhöft, Application Development & Technical Service Engineer - Key Learning Objectives | What does a higher SDR class mean in practice?
– Get to know Polybutene-1 for use in pressurized hot and cold water pipe systems
– Learn about the extraordinary characteristics of this most technically advanced thermoplastic material
– What are the benefits of using PB-1 in pipe systems against alternative thermoplastic materials?
– Opportunities to reduce the operational costs over the lifetime of a pipe system
Webinar: Benefits of PB-1 for pressure piping systems
– What does a higher SDR class mean in practice?