The main benefits of PB-1:
Higher Standard Dimension Ratio (SDR):
Thinner walls without sacrificing pressure capabilities.
Significant material and weight savings per meter.
Enhanced Flow Rates:
Larger internal diameters enable higher flow rates at the same pressure.
Reduced energy needs and operational costs.
Superior Design Flexibility & Acoustic Performance:
Design versatility with all jointing techniques (push-fit, butt fusion, etc.).
Exceptional acoustic properties for quieter systems.
Environmental Sustainability:
Less material use contributes to a reduced carbon footprint.
Demonstrates commitment to sustainable building practices.
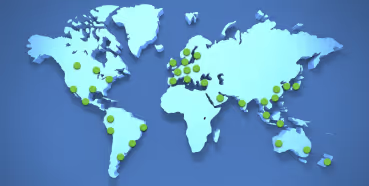
All PBPSA members are leaders in their respective markets including the production of PB-1 material grades, and the manufacture and marketing of piping and component systems worldwide.
contact our membersDetailed benefits of Polybutene piping systems compared to PE-RT and PEX
For building projects, the true cost variation of piping systems across competing materials is more than a per length cost comparison for the same outside pipe diameter.
A true cost comparison between piping systems should include installation time, jointing options, life span and SDR rating.
Specifiers look at: ease of installation impacting onsite costs; jointing options, long-term system performance and projected life span; and Standard Dimension Ratio (SDR) comparing pipe materials for durability against pressure.
When compared to PE-RT and PEX systems, PB-1 offers significant benefits across a broad range of performance categories all contributing to make PB-1 piping systems the optimum choice for high performance piping installations.
Standard Dimension Ratio (SDR)
The SDR or the Standard Dimension Ratio refers to the geometry of a pipe. SDR is a method of rating a pipe's durability against pressure and it describes the correlation between the pipe dimension and the thickness of the pipe wall. SDR 11, for example means that the outside diameter of the pipe is eleven times the thickness of the wall.
- High SDR ratio:
- The pipe wall is thin compared to the pipe diameter
- Low SDR ratio:
- The pipe wall is thick compared to the pipe diameter
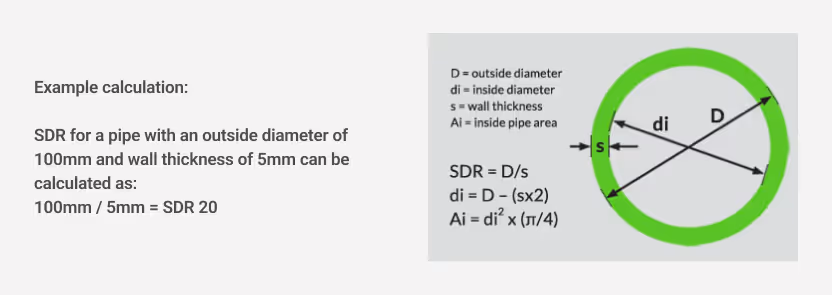
SDR rates pipe durability against pressure and correlates a pipe's outside diameter and wall thickness.
Why does SDR matter for piping systems?
Due to the higher SDR ratio of PB-1 compared to either PE-RT and PEX, PB-1 piping systems deliver the following benefits because of its lower wall section requirements for the same pressure rating and outside pipe diameter:
- Less material for the same pressure capability
- Less weight per meter of pipe
- Lower outside pipe diameter for the same performance
- Larger inside area for the same outside diameter providing:
- Higher flow rate at the same pressure
- Lower pressure loss, requiring less energy to run a system or pumps with lower capacity
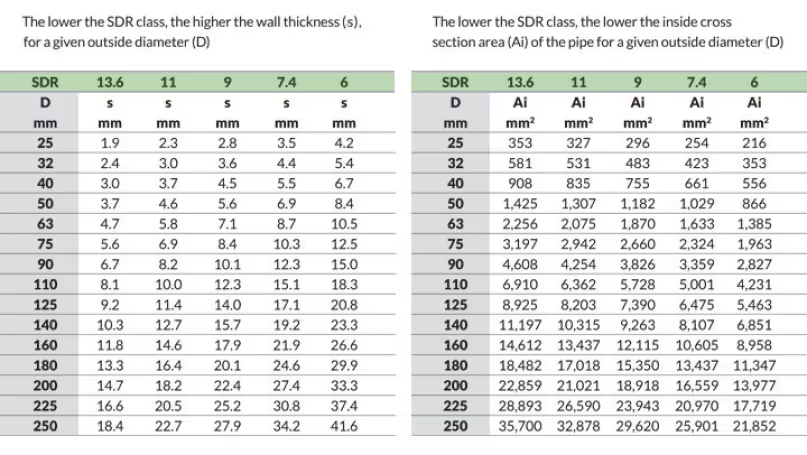
SDR Classes and Pipe Dimensions
SDR classes quoted in National Standards for District Energy piping systems
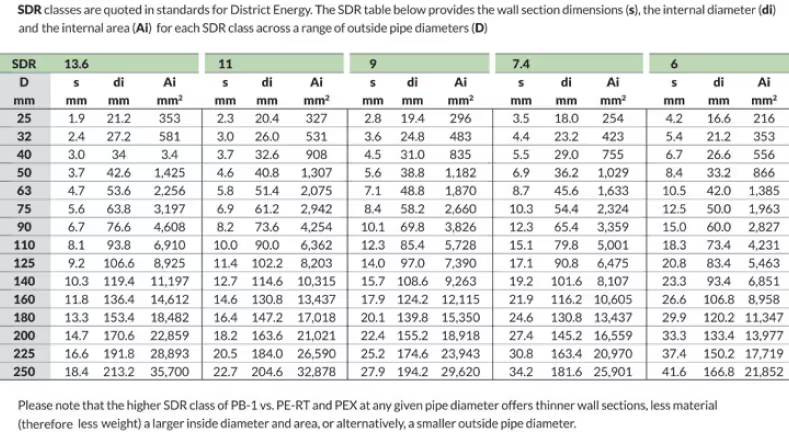
SDR Classes and Water Hammer
A column of moving water within a pipeline contains stored kinetic energy arising from its mass and velocity. Since water is essentially incompressible, this energy cannot be absorbed when a valve is suddenly closed.The result is a high instantaneous pressure surge normally referred to as 'Water Hammer'.
The higher the SDR Class the lower the water hammer at a given flow rate. PB-1 has the highest SDR Class compared to PP-H, PP-R, PE-RT and PEX
With people living together in greater density the noise levels and acoustic properties of piping systems are a significant issue. Piping systems that minimise fluid noise and water hammer where pipework passes through ceilings and walls are a key element in addressing residents’ noise concerns.
The maximum theoretical value of pressure surge Ps is:
v0 · a · ρ = ps
v0 = velocity of the medium [m/s]
a = propagation rate of the pressure wave [m/s]
ρ = density of the medium [kg/m³]
ps = pressure surge – water hammer [N/m²]
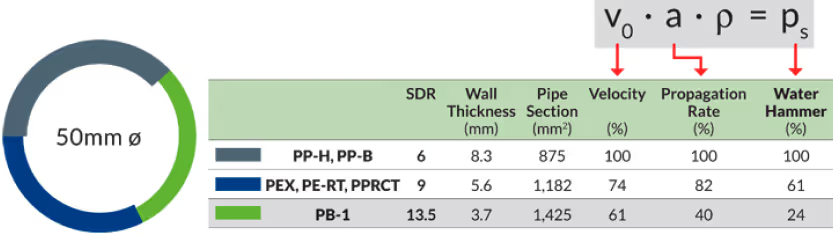
The maximum surge pressures caused by water hammer can be calculated using the following equation taken from the 'Handbook of Thermoplastic Piping System Design', Thomas Sixsmith and Reinhard Hanselka, Marcel Dekker Inc., pp 65-69
Ps = V((3960 E t)/(E t + 3 x 105 DI))½
where:
Ps = surge pressure (psi)
V = water velocity (ft/sec)
DI = inside diameter of the pipe (in)
E = modulus of elasticity of the pipe material (psi)
t = pipe wall thickness (in)
The low elastic modulus of Polybutene-1, combined with reduced wall thickness gives rise to a low surge pressure for a given pipe OD and pressure rating. The table below compares maximum surge pressure for 38.1 mm (1-1/2") OD pipes of different plastic materials, designed for the same pressure service.
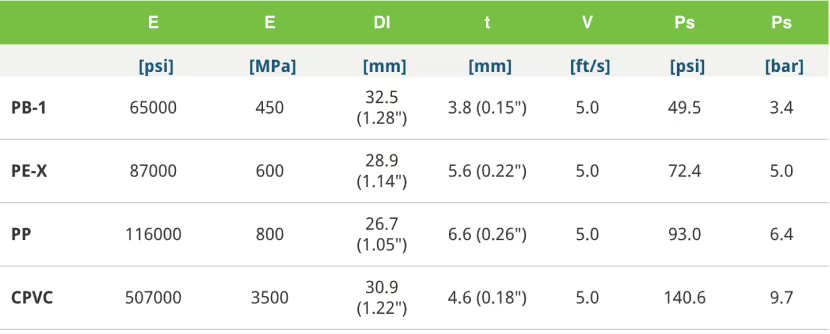
When compared to PP-H, PP-B, PE-RT and PEX, PB-1 has the highest SDR Class and delivers the best acoustic capabilities including the lowest level of water hammer.
National standards: the source for piping dimensions comparing materials PB-1, PE-RT and PEX
With people living together in greater density the noise levels and acoustic properties of piping systems are a significant issue. Piping systems that minimise fluid noise and water hammer where pipework passes through ceilings and walls are a key element in addressing residents’ noise concerns.
Read more here