Installation simplicity delivers quality and speed
Piping systems from Polybutene-1 have revolutionised how hot and cold water pressurised systems are installed. With the installation of PB-1 piping, no bending tools, no naked flame, and no fluxes or chemicals are needed.
PB-1 offers superior on-site handling due to its high flexibility, low weight, reduced pipe wall thickness and low memory effect.
PB-1 installation benefits
- Long flexible pipe in coils means less connections
- Few tools required and no flame, heat or fluxes needed
- Lightweight, flexible PB-1 piping in coils is easy to ship and handle on site
- PB-1 systems' suppliers provide complete systems, optimising performance and jointing integrity
- Multiple systems choices are available for specific project needs and jointing options
Polybutene-1 offers superior handling due to its flexibility, reduced pipe wall thickness and low memory effect. In addition to the potential cost savings of faster installation, PB-1 pipes provide significant benefits for projects requiring installations in tight, cramped spaces.
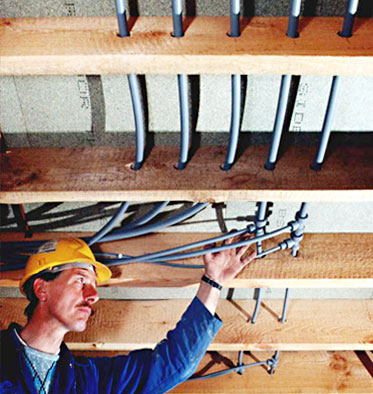
Simplicity of installation means faster onsite turnaround times and lower overall project costs.
Pipework of up to 50mm in diameter is supplied in lightweight and easily handled coiled lengths of up to 500 metres. Installations can be made in suspended floors from below before ceilings are fitted and flexible PB-1 pipe can be cabled around obstructions and through joists significantly reducing the number of joints.
Continuous, flexible pipe with fewer joints means optimum system integrity and faster installation. With PB-1, many installations can be made without accurate pre-measuring, since it is easy to measure and cut in situ. Also, the light weight and ease of handling of PB-1 piping allows pre-fabrication and rapid on-site installation for project locations where business down-time is critical.
Since the first successful European installations in the 1970's, advances in material technology, manufacturing and sophisticated new product systems; along with national and international standards protocols, has advanced the performance of PB-1 piping systems even further.
Modern jointing technology for Polybutene-1 piping systems, whether prefabricated in the workshop, or carried out on the building site, provides easy, safe and efficient installation which is therefore more cost-effective.
There are four possibilities for joining pipes made from Polybutene-1 with fittings. These are:
- Socket fusion (1)
- Compression (2)
- Electrofusion (3)
- Push-fit (4)
With PB-1, many installations can be made without accurate pre-measuring, since it is easy to measure and cut in situ. Also, the light weight and ease of handling of PB-1 piping allows factory prefabrication and rapid on-site installation.
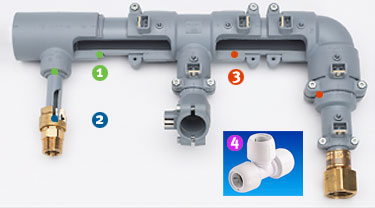
The socket fusion method for connecting Polybutene-1 pipes and fittings is designed for off-site prefabrication. Sub-assemblies such as basement manifolds and riser pipe systems can be prefabricated in a workshop environment. To achieve consistently acceptable welds, it is important that the temperatures and times of welding and the procedures for bringing the pipe and fitting components together to produce the weld are precisely controlled. This can only be achieved when the required equipment is operated under workshop conditions. The light weight of PB-1 means that prefabricated sub-assemblies can be easily transported to the project site, and installed quickly and efficiently.
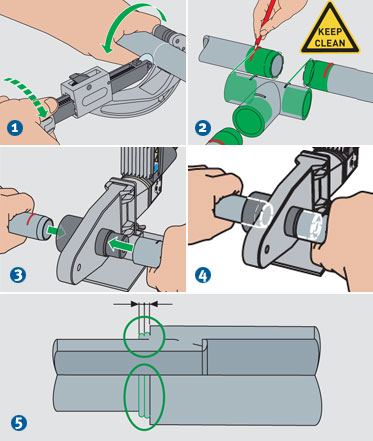
Off-site pre-fabrication can be an added advantage on busy building sites where efficient scheduling of the various sequences of construction is key to meeting project deadlines or for installations at commercial and industrial locations where interruption of normal operations can be expensive and disruptive.
- Ideal for prefabrication
- Cuts material costs and installation time
- Full PB-1 solution
Mechanical compression fittings are used when Polybutene-1 pipe needs to be connected to metal system components. Compression fittings are designed with the unique characteristics of PB-1 in mind. By separating the sealing and clamping areas of the fitting, a tension-free, durable and leak-proof connection between pipe and fitting can be achieved without the use of an elastomeric seal. Due to the creep behaviour as well as the flexural strength and heat resistance of PB-1, the connection can be subjected to temperature and pressure stress immediately after installation is completed.
- No special tools required
- Low creep behaviour
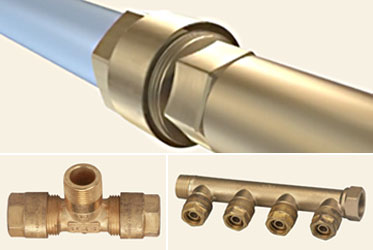
Polybutene-1 electrofusion fittings have a moulded-in wire heat-fusion coil and plug connector. The coil lies just below the surface of the area to be welded to the pipe. Once the pipe is in position, an electrically operated fusion device is connected to the fitting via the plug.
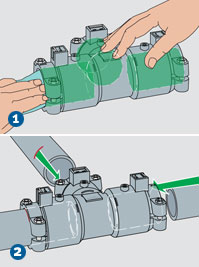
This fusion device automatically measures the resistance in the heating coil to determine the type and dimension of the fitting. An appropriate current is then passed through the heating coil for a precise time to provide optimum welding temperature conditions. When the weld is complete, the device produces a signal which indicates the pipe and fitting can then be disconnected.
The welding process is shown below (L-R)
- Clean the fitting
- Place the pipe into the fitting and tighten the screws to fix the pipe
- Insert plugs into connection weld points and start process using system fusion unit
- Use indicator to check weld

This system produces consistent quality, high performance welds and has delivered excellent long term service reliability. The fusion device is small enough to operate on site in confined spaces - all that is required is a source of electricity. For larger pipe sizes, electrofusion is often used to produce prefabricated assemblies in a workshop environment.
- Easy, fast and very reliable
- Prefabrication is possible
- Good fitting access for constrained areas
- Full PB-1 solution
GF electrofusion installation instructions INSTAFLEX | INSTABIG
Polybutene-1 push fit plumbing systems are quick to install, without the need for tools, glues or heat. They may be used on plastics pipe or copper tube, provided the manufacturers instructions are followed.
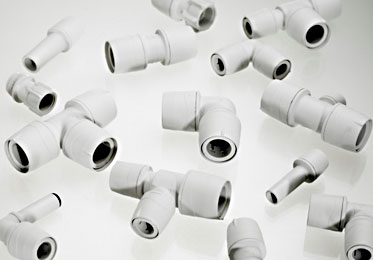
Push fit systems are suitable for use in most plumbing and heating installations including hot and cold water and underfloor heating applications. Push fit is also applicable for a wide range of contract and retrofit projects and is particularly suitable for first fix installations.
Push fit features a one step jointing operation for quick and easy installation. Certain systems allow joints to be adjusted during the installation process, or demounted by using a special release tool.
All PB-1 push fit fittings include four basic elements:
- Fitting body, in which all the components are housed, together with a cap (which may or may not be removable) to hold the components in the fitting
- A sealing mechanism, usually either an 'O' ring or ring seal
- An integral gripping mechanism which permanently grips the pipe firmly in position
- A support sleeve which fits into the end of the pipe to prevent deformation when the pipe is inserted into the fitting
Although push fit fittings are simple to use, there are basic steps which must be taken to ensure an effective joint is made:
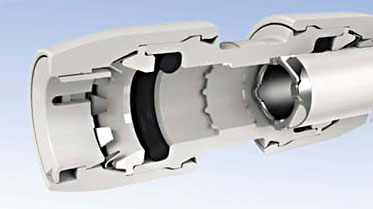
- Pipes carry depth insertion marks at intervals along the pipe. The pipe should be cut square at a depth insertion mark, using a purpose-designed cutter. The end should be free of swarf.
- The support sleeve should be inserted into the pipe end
- The pipe should be pushed firmly into the fitting until the next depth insertion mark reaches the end of the cap
- The pipe should be tugged back, to ensure that the gripping mechanism has engaged on the pipe.
The manufacturer's installation instructions should always be closely followed when installing push fit fittings.
The butt fusion method for connecting Polybutene-1 pipes and fittings is mostly utilised for larger pipe diameters. Butt fusion is possible up to very large diameters and very thick wall sections. To achieve consistently high quality welds, precise control is required for welding temperatures, times and pressures and surface interface between pipes and fittings in line with the instructions of the pipe system manufacturers.
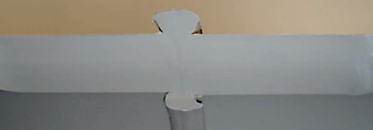
Butt fusion machines applicable to variable pipe diameters clamp both pipes accurately and perform the following essential functions to create a strong butt joint per the images below (L-R).
- Left: Both pipes are clamped to ensure they are accurately aligned. The surfaces of both pipes are shaved simultaneously to ensure they will butt cleanly with full surface contact.
- Centre: A heating plate is inserted for a prescribed time and both pipes contact the sides of the heating plate surfaces under compression.
- Right: The heating plate is removed and the two heated pipe surfaces come together under the correct compression and time period as specified by the machine to create a strong integral bond.
