Polybutene-1 offers advantages for complex piping systems specified for high-rise buildings
Cities around the world are growing at a rapid rate. Over 50% per cent of the world’s population lives in urban areas and that percentage is expected to increase to 66 per cent by 2050. UN projections indicate that urbanization, combined with the overall growth of the world’s population, could add another 2.5 billion people to urban populations by 2050.
Compared to PVC-C, PEx, PP-R, PP-RTC and PE-RT, Polybutene piping systems deliver higher performance for pressure resistance, impact toughness, water hammer resistance, flexibility and low expansion force.
For practical reasons such as lifespan and ease of installation, building codes around the world for high rise buildings are approving the use of plastic piping systems.
When designing piping systems for high rise buildings, plumbing engineers must consider the elevated pressures required for the water supply and distribution systems, in addition to general drainage and venting. The height of a building affects the forces applied to plumbing systems. That means conventional designs and piping materials are often not adequate for the job. This relates to pressure piping in the water supply system, and also the drainage system. In a high-rise building, a well-designed water supply system should operate without the user being aware of its existence.
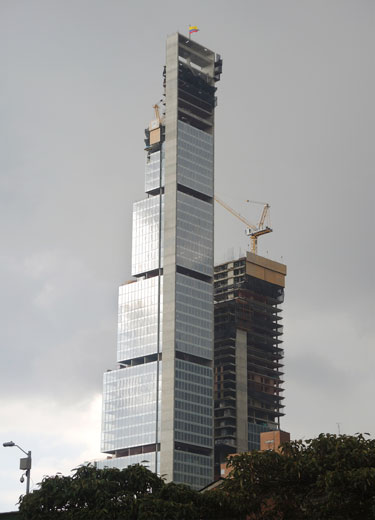
These requirements are essential to achieve a safe, usable and reliable system:
- The system (pipe-fitting-union) should withstand the high pressure due to the high-water column
- The system and material should be adequately flexible to withstand the water hammer that occurs during the lifespan of the installation
- High level of resistance against tensions on pipes and fittings due to expansion e.g. in risers
- The piping system should offer easy, secure and economical assembly technologies
- Extensive product range in order to design an entire project in one single material across piping diameters from small to large
- Easy and reliable expansion control by using small expansion loops, etc.
Compared to PVC-C, PEx, PP-R, PP-RTC and PE-RT, Polybutene-1 (Polybutylene, PB-1) piping systems deliver higher performance for pressure resistance, impact toughness, water hammer resistance, flexibility and low expansion force making it the optimal choice for engineers in the design of high-rise piping systems.
For all high-rise buildings, whether office, condominium, hotel or hospital, the design challenges multiply based on the functional complexity. Typically, hospitals and hotels require a higher density and complexity of piping systems and plumbing fixtures than most other types of buildings and Polybutene-1 piping systems offer significant benefits to that sector.
Case study: BD Bacatá - Bogotá
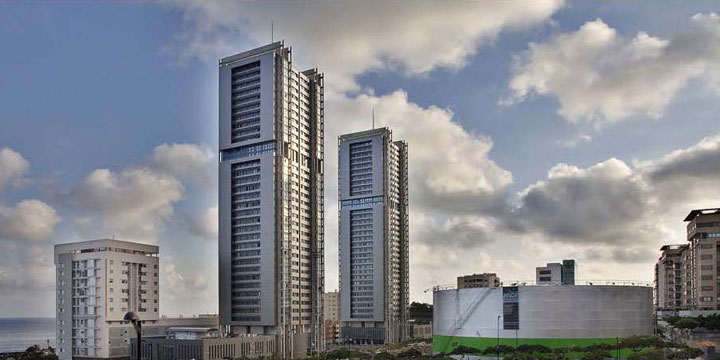
PB-1 High Rise Project: Torres Santa Cruz – Nueva Terrain
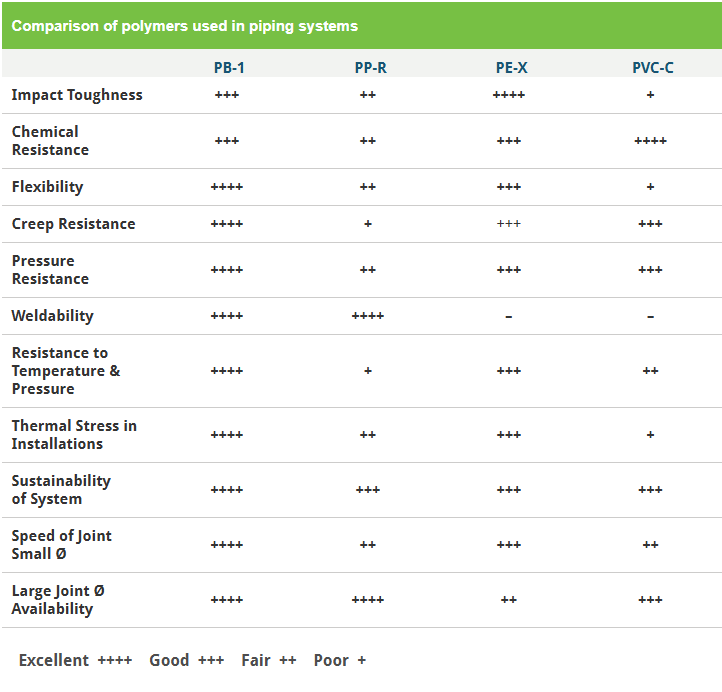
The ideal choice for pressurised piping systems
The property combination setting PB-1 apart from competitive materials is its high flexibility combined with outstanding resistance to internal pressure creep resistance over a wide range of temperatures.
The unique morphology and crystallisation behaviour of PB-1 gives it unrivalled properties for pressurised piping systems.
All polyolefinic materials tend to creep when exposed to continuous stress over a long periods of time.
This cold flow behaviour can be suppressed by creating a 3-D network in the polymer structure such as the physical and chemical linking utilised in the manufacture of Polyethylene (PE-X). Polybutene-1 however, displays superior inherent creep resistance without the need to apply any additional cross linking, copolymerisation or compounding modification.
In its simplest homopolymer form, the property profile of Polybutene-1 makes it the ideal choice for satisfying the demands of hot and cold pressure piping systems applications.
The performance comparison of PB-1 and alternative plastics materials
Parallel standards to ISO 12230 exist which present the effect of time and temperature on the expected strength of the materials listed below. The data presented in these standards provides a useful means of comparison of the performance of these alternative plastic materials used for piping systems.
The following figure shows the performance reference lines (pressure resistance properties) for the following materials at 70°C on an equivalent scale:
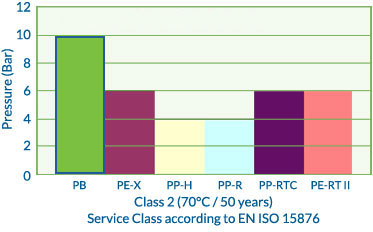
Best performing materials
- PB-H - ISO 12230 (2012)
- PB-R - ISO 12230 (2012)
Medium performing materials without knee point
- PE-X - ISO 15875 (2003)
- PP-RCT - ISO 15874 (2013)
- PE-RT type II - ISO 12230 (2012)
Low performing materials with knee point
- PE-RT type I - ISO 22391 (2009)
- PP-R - ISO 15874 (2013)
After 10 years of exposure to continuously applied stress, the best performing Polybutene-1 (PB-H & PB-R) retains over 50% more strength than the medium performing materials (PE-X, PP-RCT & PE-RT type II) and 70% - 90% more strength than the lower performing materials PE-RT type I and PP-R.
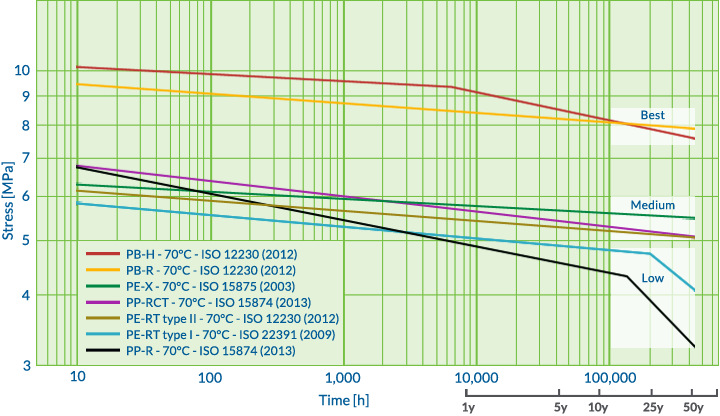
Design stress
By employing standardised dimensional criteria presented in ISO 10508 it is possible to calculate the maximum allowable hoop stress of these alternative polyolefin pipes for the various standardised applicational temperature classes. This calculation of design stress results in the comparison presented in the table below which shows that PB-1 polymers achieve the highest hoop stress values across all standardised application classes. The intrinsic stress bearing advantage of PB-1 is between 35% and 90% higher, depending on application class and material. This effectively means that at equivalent thickness, PB-1 pipes offer a significant safety factor over these alternative plastic materials for installed systems.
After 10 years of continuously applied stress, PB-1 retains over 50% more strength than PE-X, PP-RCT and PE-RT type II, and 70-90% more strength than PE-RT type I and PP-R.
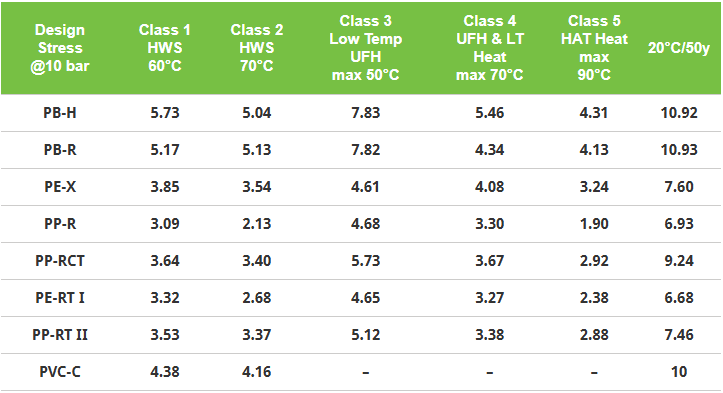
From the maximum allowable hoop stress, we can calculate a minimum allowable wall thickness. It is clear from the calculation that Polybutene-1 pipes can be produced with a significantly reduced wall thickness when compared to other materials dependent on applicational standards limitations. Lower wall thickness also means a larger internal bore for a given external pipe diameter resulting in reduced head pressure loss and lower flow speeds to deliver a fixed volume of water.
*PE-RT denotes Raised Temperature Resistance polyethylene
Superior long term creep resistance
In contrast to other thermoplastics used in piping applications, performance modification via compounding, cross-linking or copolymerisation is not necessary for PB-1 piping systems to fulfil the stringent performance standards applied to their use.
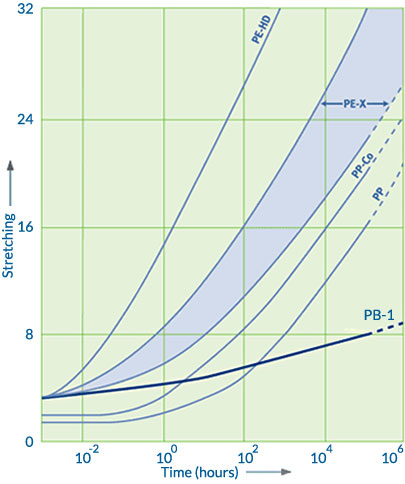
In comparison with other polyolefin materials, Polybutene-1 has a higher level of resistance to strain under continually applied stress over long periods of time.
This is known as creep behaviour and the graph illustrates the superior performance of PB-1 at times in excess of 100 hours.
In addition to its excellent mechanical and thermal properties, PB-1 provides a high level of resistance to chemical attack and also offers a level of flammability resistance meeting the demands of most applications.
In its most simple homopolymer form, the balance of properties of PB-1 make it the technically preferred material for the production of pressurised hot and cold water piping systems.
Pipe weight and hydrostatic efficiency
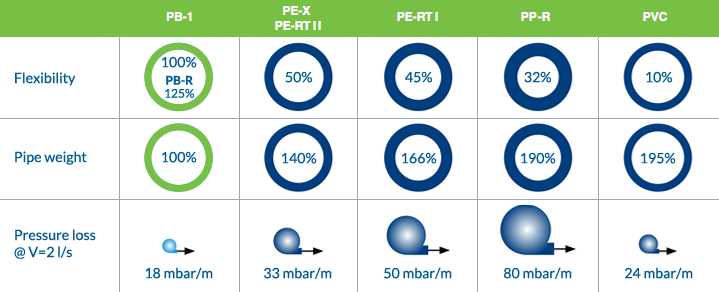
Calculated for application class 2, 10 bar design pressure, based on published data.
Acoustics is among the superior properties of Polybutene-1 piping systems
With people living together in greater density and with increased expectations of comfort, noise levels and acoustic properties of piping systems are a significant issue with high-rise buildings. Piping systems that minimise fluid noise and water hammer where pipework passes through ceilings and walls are a key element in addressing residents’ noise concerns.
With Polybutene-1 water hammer arrestors are not required reducing installation and maintenance costs.
Pressure systems in high-rise buildings are also an important factor. Properly-functioning pressure systems are essential to ensure the comfort of inhabitants, who expect to be able to take a shower at the right temperature and with the right pressure, at any time.
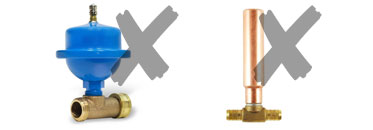
Planners and developers are concerned with avoiding noise with longer pipe runs and higher loading in increasingly open and connected buildings where many residents may occupy the building. A building is interconnected by the branch and stack pipes. In a 50-storey building the sound would travel from the base to the top of the pipe in under 0.5 seconds.
There are multiple causes of noise generation in the plumbing system:
- Type and quality of faucets
- Water flow velocity through pipes, valves and filters
- Density of the piping system material (softer is better)
- The piping fastening technology (including brackets with rubber inliners)
- Whether concealed pipes in the wall are insulated – or not
- Whether tap-elbow connectors inside the wall are insulated – or not
Sound dampening
Among the superior properties of Polybutene-1 in comparison with other materials its excellent sound dampening. The combination of thinner pipe wall construction, low elastic modulus and low specific density in Polybutene-1 pipes (ρ = 0.9 g/cm3) leads to high absorption of “water hammer” and other noises associated with heating and cooling in pipe systems. Tests showed a 90% reduction of pipe-borne noise in the Royal Albert Hall in London after the installation of PB-1 pipes.
The thinner pipe walls, high elasticity and low specific density in PB-1 pipes leads to high absorption of operating noises.
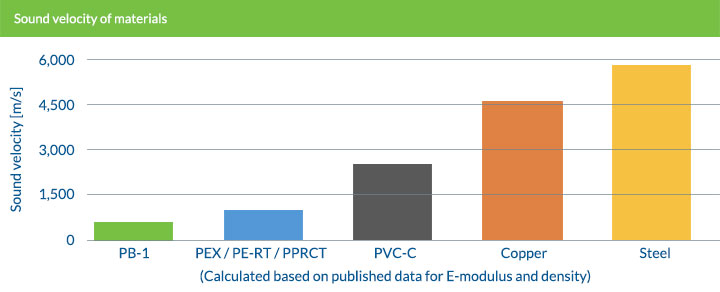
Resistance to Water Hammer
A column of moving water within a pipeline contains stored kinetic energy arising from its mass and velocity. Since water is essentially incompressible, this energy cannot be absorbed when a valve is suddenly closed.
The higher the SDR Class the lower the water hammer at a given flow rate. PB-1 has the highest SDR Class compared to PP-H, PP-R, PE-RT and PEX
The result is a high instantaneous pressure surge normally referred to as 'Water Hammer'.
With people living together in greater density the noise levels and acoustic properties of piping systems are a significant issue. Piping systems that minimise fluid noise and water hammer where pipework passes through ceilings and walls are a key element in addressing residents’ noise concerns.
Five factors determine the severity of water hammer:
- Velocity
- Modulus of elasticity of the pipe material
- Inside diameter of the pipe
- Wall thickness of the pipe
- Valve closing time
Repetitive water hammer can be destructive to pipe systems. Beside the noise, water hammer can cause pipelines to break if the pressure is high enough.
The maximum theoretical value of pressure surge Ps is:
v0 · a · ρ = ps
v0 = velocity of the medium [m/s]
a = propagation rate of the pressure wave [m/s]
ρ = density of the medium [kg/m³]
ps = pressure surge – water hammer [N/m²]
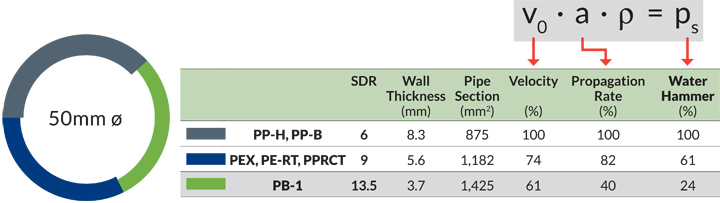
The maximum surge pressures caused by water hammer can be calculated using the following equation taken from the 'Handbook of Thermoplastic Piping System Design', Thomas Sixsmith and Reinhard Hanselka, Marcel Dekker Inc., pp 65-69
Ps = V((3960 E t)/(E t + 3 x 105 DI))½
where:
Ps = surge pressure (psi)
V = water velocity (ft/sec)
DI = inside diameter of the pipe (in)
E = modulus of elasticity of the pipe material (psi)
t = pipe wall thickness (in)
The low elastic modulus of Polybutene-1, combined with reduced wall thickness gives rise to a low surge pressure for a given pipe OD and pressure rating. The table below compares maximum surge pressure for 38.1 mm (1-1/2") OD pipes of different plastic materials, designed for the same pressure service.
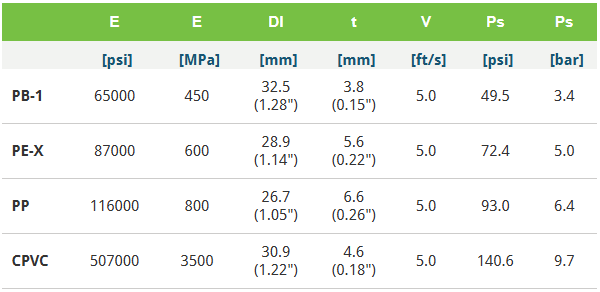
When compared to PP-H, PP-B, PE-RT and PEX, PB-1 has the highest SDR Class and delivers the best acoustic capabilities including the lowest level of water hammer.
Superior thermal performance in challenging conditions
Resistance to freezing conditions
Polybutene-1 piping systems have lower thermal diffusivity than copper pipes and this means water takes longer to freeze in them during inclement weather. If water does freeze, the pipe expands to take account of the added volume, returning to its normal dimensions when the thaw arrives.
Case study: Säntis 2000 – Switzerland.
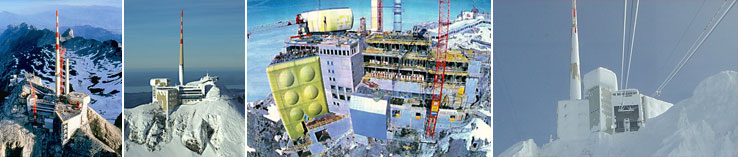
Designed to withstand high heat and high pressure – 24/7
The same characteristic that slows the speed at which water can freeze within Polybutene-1 pipes also results in them remaining cool to the touch, even when high temperature water is running through them. This can be an added benefit particularly where children or the elderly and infirm are among a building's occupants.
For high-rise piping systems, all risers can be made using the PB-1 systems (up to 50mmØ using Pushfit systems and up to 225mmØ using Electrofusion jointing) offering a very high level of pressure resistance. Hot water supply for hotels can be designed for central hot water heaters to distribute hot water to all bathrooms through the risers.
These risers must withstand high pressure rates not only because of the long water columns typical in high-rise buildings, but also due to the 24 hour hot water return lines that can create significant challenges for certain plastic piping systems.
Under such extreme operating conditions, PB-1 piping systems offer engineers the longest lifetime for piping installations.
Benefits vs. traditional metal pipes
In addition to lower thermal diffusivity vs. metal, PB-1 piping and plumbing systems will not scale-up in hard water areas or corrode in soft water areas. As mentioned, they absorb and suppress sound, rather than transmitting it. They are not subject to 'water hammer' which can otherwise be a problem, particularly in areas noted for high water delivery pressures.
Cost effective performance
Due to the reduced requirement for fittings due to the flexibility and length of PB-1 piping (delivered in coils), installations plumbed using flexible systems are highly cost-effective. In terms of system performance, flexible ranges offer excellent longevity, making them a good long-term investment.

Flexible plumbing systems are increasingly the technology of choice for hot and cold water services, central and underfloor heating and cooling installations in domestic, commercial and industrial environments because of their convenience, performance and durability.
Systems quickly evolving to meet new standards and building codes
The evolution of the PB-1 plumbing systems continues at a rapid pace as manufacturers extend and modify systems in response to rapidly changing building requirements and codes. They are extensively specified for residential, commercial and industrial environments because of their convenience, performance and durability.
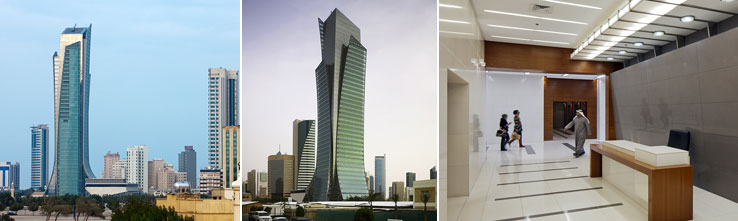
Ensuring the delivery of best quality drinking water
To satisfy the highest quality requirements drinking water piping systems, specifiers must consider the most challenging in-use scenarios to ensure the delivery of best quality drinking water. The decision also needs to factor in-depth comparisons across plastics categories as well as future perspectives in installation and joint techniques.
Polybutene-1 is regarded as an optimum material for drinking water plumbing & piping systems.
Taken overall, Polybutene-1 is regarded as an optimum raw material for drinking water systems due to the fact that PB-1 is a partially crystalline polyolefin thermoplastic with a high long-term performance and a high resistance to flow at high temperatures – properties that are essential for interior hot and cold water installations as well as for heating.
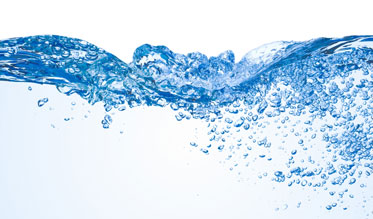
Polybutene-1 is the universal plastic material that allows joints by fusion welding and by mechanical fittings, combining numerous favourable characteristics such as:
- Best in class dimensional stability and high long-term performance
- High resistance to plastic flow, significant for the watertightness of compression joints
- Resistance to hot water up to 95°C.
- Stabilization against alteration due to ultraviolet rays during handling and installation
- Pigmentation against the formation of algae
- High flexibility, even at low temperatures
- Low embrittlement temperature
- High resistance to impact and water hammer
- High resistance to abrasion
- As a consequence of its high resistance to high temperatures compared to other plastics, PB-1 allows lower wall thicknesses for identical usage profiles which, in addition, is converted into larger internal transport diameters for the same external diameter, lower velocities for the same flow, lower head losses and a lower pipe weight per metre.
- Excellent energy audit compared to other materials makes it the product with the lowest environmental impact among those of the same application
Advantages of PB-1 for drinking water piping and plumbing systems
Polybutene-1 systems of pipes and fittings for the indoor distribution of hot and cold drinking water and heating offers the following advantages:
- Absence of corrosion
- Absence of scaling
- High stability upon ageing even at high temperatures
- Quick, easy and safe joints
- Wide range of fittings
- Possibility of complete projects in the same material and system, with diameters from 15 mm to 160 mm
- Safe and hygienic
- High pipe flexibility, leading to quick and easy assembly and installations
- Simple, effective and economical installation techniques
Flexible pipe coils for large and small diameters revolutionises installation
The inherent high flexibility and light weight of PB-1 pipe makes the use of coiled pipes a reality. PB-1 pipe flexibility also reduces installation time because joints and fittings are not always needed at every direction change of the piping within the floor plan and wall layout.
The inherent flexibility of coiled PB-1 piping, allows an efficient plumbing installation process – similar to electrical wiring.
The flexible PB-1 coil length of 100m versus 5m for rigid PVC piping lengths saves a significant amount of cutting, joining and fittings. Manufacturers have also introduced packaging that allows pipe to be progressively dispensed to the project at hand from the pack; allowing easy storage or transport to the next task onsite.
The availability of long pipe lengths means that the number of joints in a given system are significantly reduced, delivering benefits in installation time and long-term system reliability.
This feature, coupled with the inherent flexibility of PB-1 pipe, allows plumbing to be installed throughout a high-rise building structure on each level in much the same way as electrical wiring. Pipes can also be readily routed through or encapsulated in building elements such as walls, ceilings or floors and also allowing the “pipe-in-pipe” or “spider” method (spider method = manifold overhead in the false ceiling with downpipes to the tap points). This latest generation approach to plumbing systems has created a major change in the way building projects are now estimated and delivered with benefits flowing to all sectors of the construction process through to end-users.
New techniques benefit from flexible plumbing
There are also safety benefits due to PB-1 jointing systems not requiring heat or flame – hence no fire risk. This is a particular advantage where space is restricted or the surrounding environment is potentially flammable.
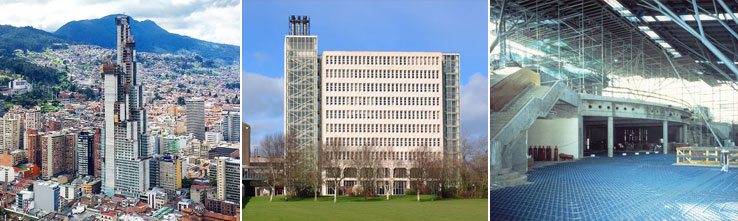
Installation simplicity delivers quality and speed
Piping systems from Polybutene-1 (Polybutylene, PB-1) have fundamentally changed how hot and cold water pressurised systems are installed. With the installation of PB-1 piping, no bending tools, no naked flame, and no fluxes or chemicals are needed.
With the installation of PB-1 piping, no bending tools, no naked flame, and no fluxes or chemicals are needed.
Modern jointing technology for Polybutene-1 piping systems, whether carried out on the building site, or prefabricated in the workshop, provides fast, safe and efficient installation, and as a result is more cost-effective.
There are four primary possibilities for joining pipes made from PB-1 with fittings. These are socket fusion, compression fittings, electrofusion and push-fit plumbing systems. Large diameter pipes can also be joined using butt fusion.
Socket Fusion
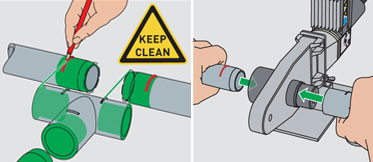
The socket fusion method for connecting Polybutene-1 pipes and fittings is designed for off-site prefabrication. Sub-assemblies such as basement manifolds and riser pipe systems can be prefabricated in a workshop environment. The light weight of PB-1 means that prefabricated sub-assemblies can be easily transported to the project site, and installed quickly and efficiently.
Compression
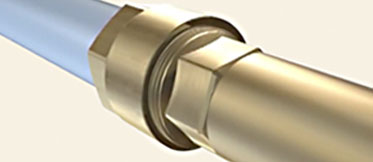
Mechanical compression fittings are used when Polybutene-1 pipe needs to be connected to metal system components. Compression fittings are designed with the unique characteristics of PB-1 in mind.
- No special tools required
- Low creep behaviour
Electrofusion
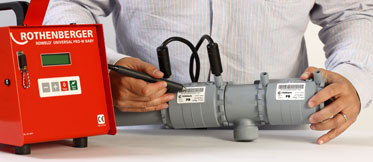
Polybutene-1 electrofusion fittings have a moulded-in wire heat-fusion coil and plug connector. The coil lies just below the surface of the area to be welded to the pipe. Once the pipe is in position, an electrically operated fusion device is connected to the fitting via the plug. This system produces consistent quality, high performance welds and has delivered excellent long term service reliability.
Push Fit Systems
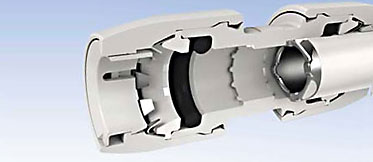
Polybutene-1 push fit plumbing systems are quick to install, without the need for tools, glues or heat. They may be used on plastics pipe or copper tube, provided the manufacturers instructions are followed. Push fit features a one step jointing operation for quick and easy installation. Certain systems allow joints to be adjusted during the installation process, or demounted by using a special release tool.
Butt Fusion
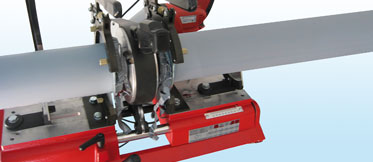
The butt fusion method for connecting Polybutene-1 pipes and fittings is mostly utilised for larger pipe diameters. Butt fusion is possible up to very large diameters and very thick wall sections. Butt fusion machines applicable to variable pipe diameters clamp both pipes accurately and create a strong butt joint.
Legionella is a bacteria occasionally naturally present in water distribution networks, and presents a potential danger to the health of the users of these installations.
The factors to combat to prevent the reproduction of this bacteria in piping systems in buildings are its reproduction temperature and the formation of a biofilm as a substrate for the feeding and colonisation of the bacteria.
The reproduction temperature of Legionella is between 20° and 50ºC, so water temperatures within this range must be avoided. On the other hand, the formation of a biofilm is aided by the accumulation of stagnant water, the temperature within the aforementioned range, the roughness of the piping and the possible corrosion of metal.
The reproduction temperature of Legionella is between 20 and 50ºC, so water temperatures within this range must be avoided.
The annihilation temperature of Legionella is established at 70ºC, and this is why thermal disinfection treatments require fluid to be heated to this temperature.
The international standards for production consider this working temperature for this application, where Class 2 is defined as applicable. The best choice of material for this problem is Polybutene-1, and with good design and appropriate maintenance of the installation, potential problems of Legionella can be avoided. PB-1 piping, due to its low roughness, the lack of corrosion, and its optimum resistance at 70ºC (annihilation temperature of the bacteria) is ideal for preventing Legionella problems. They are, in addition, suitable for annual chemical disinfection treatments (30 ppm of Cl at 30ºC, 6 bar and for 2 hours), according to tests performed by the manufacturer of the raw material, LyondellBasell in independent laboratories.
As a raw material, Polybutene-1 (Polybutylene, PB-1) has a balance of performance properties ideally suited for the building owner, project designer and installer, offering long service life of hot and cold water pressure piping systems.
Pipes produced from Polybutene-1 fulfil the stringent demands of mechanical performance and water quality requirements specified by National, European and International standards for use with potable water. This, combined with its inherent flexibility and thermoplastic properties, make Polybutene-1 an extremely versatile material for plumbing systems that offers significant benefits for piping systems required for challenging environments versus other plastics and traditional rigid pipes and fittings.

Extended service lifetime for major high-rise construction
PB-1 piping delivers a long-term plumbing system lifespan due to:
- Systems designed to withstand high heat and high pressure – 24/7
- Physical and chemical material properties (no corrosion)
- Water hammer resistance
- High resistance due to tensions and impact
- Insensitive to scale build-up and encrustation
- Resistant to freezing temperatures
- Safe and reliable jointing technologies
Meeting diverse building requirements
Polybutene-1 piping systems are now available in diameters from 10 to 225 mm, providing alternatives for a broad range of installation requirements. Whether used for large hotel, office, condominium or hospital complexes, PB-1 piping systems provide a broad array of comprehensive systems for specifiers and installers.
Piping systems made from Polybutene-1 are specified for high-rise building construction due to:
- Low thermal conductivity
- Easy use as conduit for 'pipe in pipe’ or spider methods
- Hygienic and non-toxic (potable water)
- Lightweight, flexible and manageable (coils) on-site
- Easy installation, allows bending around obstructions
- No flame or chemicals required (no fire hazard!)
- Excellent acoustic properties
- One material from entry point to last tapping point
The specification of Polybutene-1 piping systems for high rise buidings is recommended due to the following key considerations:
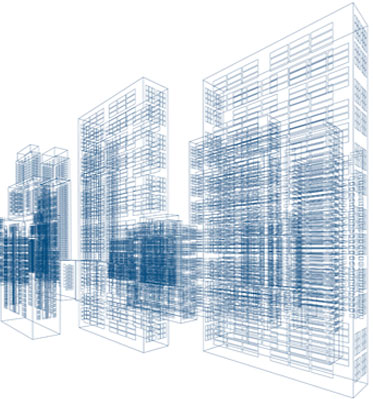
- Polybutene (Polybutylene, PB-1) is the strongest thermoplastic for plumbing and piping applications including hot and cold water at continuous high pressure for an extended service life of the installation.
- When continuous hot water running lines are specified, particularly for Hotels or Hospitals, Polybutene-1 systems are recommended because they offer the longest service life and additional benefits relating to ease of handling and installation.
- Important consideration: A small pressure increase of just 2 bar, significantly reduces the lifetime of installed piping systems. Often the reason why other plastics don't achieve their calculated and predicted service lifetimes is due to water hammer in the plumbing installation. Remember, regression curve figures are taken from static forces.
- Water hammer surge pressure affecting the pipe walls, reduces the lifetime especially when the pipe material is highly rigid. Softer and more flexible materials such as Polybutene absorb and resist water hammer at markedly improved levels compared to harder plastic materials.